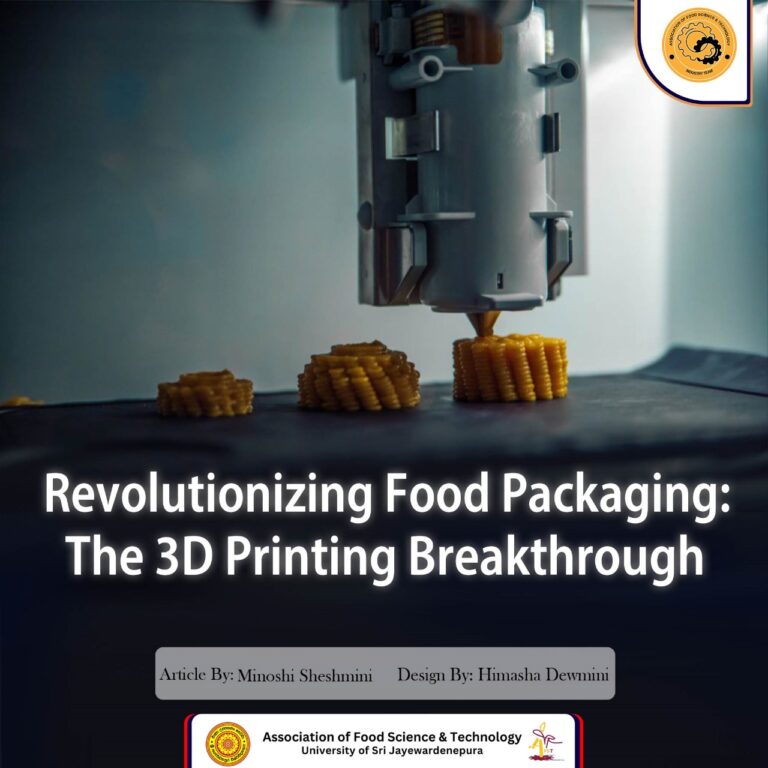
3D printing, also known as additive manufacturing is transforming the food packaging industry by enabling the creation of customized, sustainable and innovative packaging solutions. This technology builds objects layer by layer from digital designs, allowing for tailored packaging that improves product safety, reduces waste and enhances branding. It enables rapid prototyping, cost-effective development and the use of biodegradable materials, contributing to environmental sustainability. Despite challenges such as high cost and scaling issues, advances in 3D printing are improving its feasibility, offering significant benefits in design flexibility, speed to market and overall packaging efficiency. Although digital printing has been around for a while, commercial use of 3D printing has increased over the past decade, establishing it as a viable alternative to traditional manufacturing methods.
3D printing processes
3D printing technology is used to build parts of the product or create the first model in layers. The required section is designed using AutoCAD and then divided into a computerized drawing (Algorithm Draw) containing all the information and details of each layer. Each layer is constructed by distributing or blowing powder ingredients (powder) onto the surface of a previously prepared powder base layer. This process uses a technique like that used in inkjet printing, where binders are used to connect the particles and form the base powder layer. A compressor tightens each layer to stabilize it, then rises to the next layer, which is spread by binders. This process is repeated, building layer upon layer until the desired part is completely formed. A nozzle dispenses binder drops on demand to distribute binder amounts discretely or continuously over the powder layer. These materials (ceramic, metal or polymer), form a thin part of the desired shape. Materials and binders are applied sequentially and continuously until the final form is achieved.
Benefits of 3D printing
3D printing technology offers the fastest print speeds and multimedia output in days rather than hours, easily supporting the creation of multiple models at once and entire engineering departments or classrooms. Unique multi-color capabilities allow the production of realistic color models without paint, improving the look, feel and style evaluation of product designs. This technology allows text labels, logos, design ideas or images to be 3D printed directly onto models, with multiple print heads ensuring accurate and consistent colors. With a full 24-bit color, just like a 2D printer, it can produce millions of different colors. High-resolution 3D printing produces models with complex geometries and small, detailed features for complex details, such as thin walls in mechanical prototypes or rails in architectural models. Operating at a fifth of the cost of other technologies, it recycles unused materials for the next build, minimizing waste. This technology is suitable for visualization at the conceptual stages of engineering design through early-stage functional testing and does not require toxic chemicals in stereolithography. Minimal post-press finishing work is required, using the printer itself to blast the surrounding powder after printing. Bonded powders can be further strengthened by impregnating printing wax or thermosetting polymers and FDM parts can be strengthened by adding another metal. This technology is suitable for use in any standard office or school environment.
Food packaging applications
Many South African companies are waiting to prove the return on investment in 3D printing, but packaging companies have integrated it into their daily operations. They primarily use 3D printing to produce prototypes, allowing customers to see how their product will look on the shelves. Depending on the size of the model and the technology, the process of printing a part can take from a few hours to a whole day. These prototypes can be spray-painted or labeled as needed. As 3D printing technologies and materials improve, some companies are already using additive manufacturing for pilot molds, developing the ability to manufacture molds and tools for production machinery. This can lead to cost-effective customization for shorter production runs.
While some companies find it cost-effective to operate their own 3D printers, others benefit from using service bureaus that provide a range of printers and materials. Being a part of the development of 3D printing technology can provide a competitive advantage, as this technology is rapidly transforming business practices.
Future food applications
As 3D printing technology for food matures, it could revolutionize food processing in a variety of contexts. Astronauts can print their desired meals from food stored in cartridges, while adults can still benefit from bland, processed meals similar to traditional meals. This future can become a reality, if the complexities of these processes are effectively managed.
For most food applications, materials used in 3D printers must be in the form of an extricable paste or powder that can be fused by adding heat or a binding agent. The preprocessing required preparing food for printing ads complexity, which may offset some of the benefits of using this technology. A significant barrier to the adoption of 3D printing technologies is that the process is currently slower and more expensive than traditional manufacturing methods. Therefore, there needs to be a compelling reason to choose additive manufacturing. Potential advantages include the ability to offer customers products that can be easily customized, produce complex shapes or benefit from the way raw materials are stored or used.
Article by: Minoshi Sheshmini (3rd Year)
References
Haschick, J. (2018), 3-D Printing in the Food Packaging Industry, Available at: https://www.ift.org/…/3d-printing-in-the-food-packaging…
Mohamed, R.F. and Mahmoud, A.S., 2012. Emphasizing the advantage of 3d printing technology in packaging design development and production in local industries. International Design Journal, 1(1), pp.9-18, doi: https://doi.org/10.21608/idj.2012.295284
Nachal, N., Moses, J.A., Karthik, P. et al. (2019), Applications of 3D Printing in Food Processing. Food Engineering Reviews, 11, pp.123–141. doi: https://doi.org/10.1007/s12393-019-09199-8